Все, кто приезжает в Дагестан, считают своим долгом увезти с собой парочку Кизлярских ножей. По всей Республике их можно найти в любой сувенирной лавке. Казалось бы, вот он — острый, прочный и в меру гибкий инструмент с броской гравировкой, да еще и продается по доступной цене. Но на деле все оказывается не так просто.
Искусство закалять сталь: как создаются знаменитые кизлярские ножи
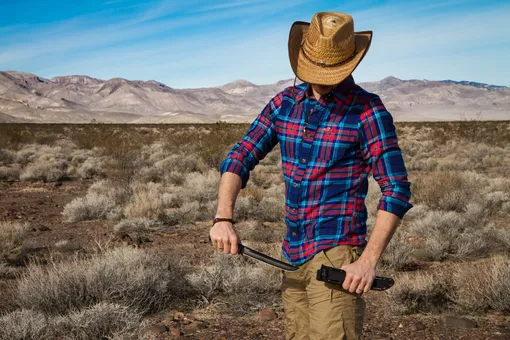
В Кизляре запущено не одно ножевое производство – работают как кустарные, так и заводы крупнее, вроде Kizlyar Supreme. Сегодня продукцию бренда стали подделывать конкуренты, - объясняет Виктор Агре, директор Kizlyar Supreme. Когда появляется достойный продукт, заручившийся авторитетом на рынке и доверием покупателя, его успех пытаются повторить другие — подражают и копируют. По словам Виктора, это закономерный процесс, и то, что везде продаются реплики Kizlyar Supreme - вполне нормально, даже хорошо, «ведь это заставляет индустрию двигаться вперед, а у пользователей вызывает желание лучше разбираться в правильных ножах».
Принцип относиться к конкурентам не как к соперникам, а скорее как к коллегам, позволяет бренду развиваться и не стоять на месте: чаще выпускать новинки, улучшать производство, обучать мастеров.
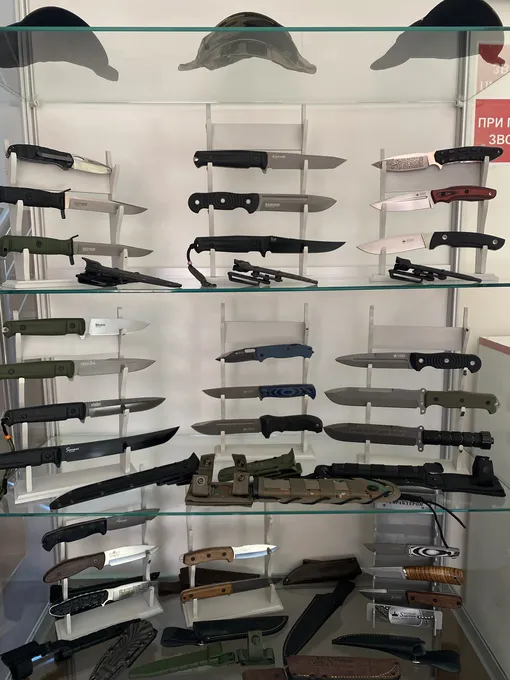
Свежий взгляд на консервативный рынок: с чего начинались кизлярские ножи
Завод Kizlyar Supreme находится в Кизляре, небольшом городке на севере Дагестана. Регион с населением в 48 тысяч человек можно назвать активным промышленным центром кизлярского округа: здесь организовано местное производство сыров и молочной продукции, разрабатывается электроника для военной и гражданской авиации и, конечно, создаются современные ножи. Попадая на завод Kizlyar Supreme кажется, что ты случайно перепутал дорогу и заглянул на частную территорию с расположенными близко друг к другу небольшими коттеджами. Дома выглядят жилыми, но мануфактуру все же выдает металлический запах и шум работающих станков ЧПУ.
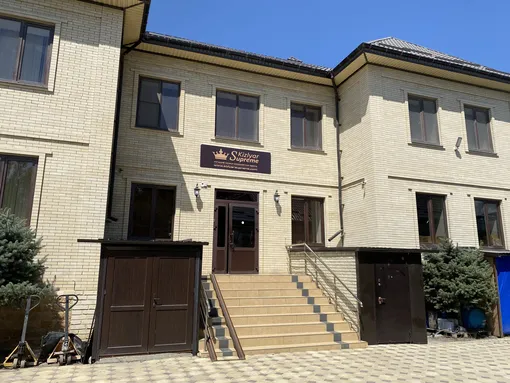
Работа на заводе не прекращается круглосуточно: первые сотрудники приходят на места в 3:00 и дежурят посменно, не забывая каждый час прерываться на отдых. Когда бренд только появился в 2011 году под руководством основателя Константина Куликова, никто и не предполагал, что вскоре предприятие начнет выпускать огромные партии, в том числе выполнять гособоронзаказ. Все начиналось с тысячи ножей в месяц.
Отойдя от дел дистрибуции продукции компании отца, владевшего крупнейшим ножевым заводом в России, Константин решил запустить собственное производство. Инициатива привела к успеху: благодаря полученному в Австралии образованию и общению с мировыми лидерами ножевого рынка Константин открыл бренд Kizlyar Supreme. В 2013 году завод стал действовать в Дагестане, где предприниматель смог на практике реализовать полученный за рубежом опыт и внедрить инновационные принципы производства.
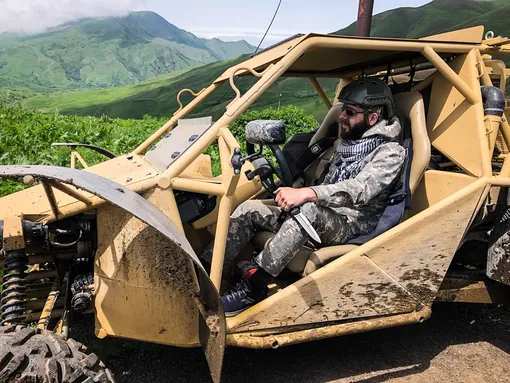
Грамотные шаги позволили увеличить оборот: в 2023 году производственных мощностей предприятия вполне достаточно для того, чтобы выпускать больше 20 000 изделий ежемесячно и одновременно с этим представлять новинки, тестировать инновационные материалы и стали.
Формула идеального ножа: все этапы производства
Сегодня завод создает качественные и долговечные ножи, прислушиваясь к мнению покупателей. В линейке компании можно найти изделия под любые задачи: тактические ножи в армейском стиле, бытовые, шейные, туристические и охотничьи, традиционные и особенно непростые в сборке — складные. Недавно под суббрендом Russo вместе с шеф-поварами Kizlyar Supreme на радость хозяйкам разработал еще и кухонные ножи из нержавеющей стали.
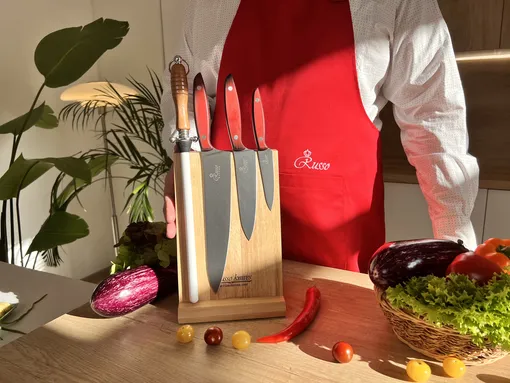
Вокруг бренда уже давно существует клуб по интересам, включающий коллекционеров и любителей ножей, которые ценят ножевую культуру и делятся своим пользовательским опытом. Ко всем пожеланиям и просьбам кизлярский завод старается прислушиваться: однажды покупатели попросили выпускать больше «Векторов» (тактический нож Vector), бестселлеров Kizlyar Supreme, — и завод закупил сталь PGK, увеличив партию. Потом клиентам захотелось увидеть модель с ручкой в цвете «олива». И это пожелание тоже было исполнено.
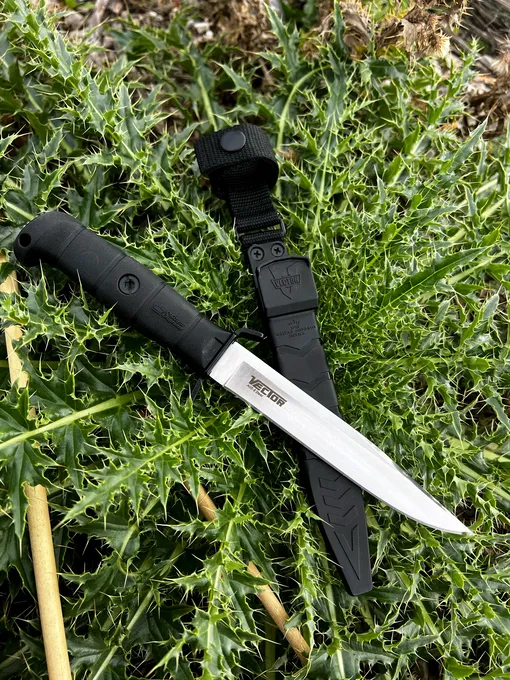
Но соответствовать запросам потребителей для компании так же важно, как просвещать потенциальных клиентов. Kizlyar Supreme ведет блог, где рассказывает, как правильно хранить ножи, ухаживать за ними и для каких целей их лучше применять в быту. А в коробку с каждым товаром помещает мини-каталог с полезными материалами и пожизненную гарантию на изделие.
Выпуская новинку, завод предусмотрительно сначала создает ее прототип, не затрачивая больших временных и денежных ресурсов, а потом тестирует, презентует на выставках и показывает потенциальным клиентам. Только получив обратную связь от людей и оценив спрос, предприятие дорабатывает модель, заново ее тестирует. Такие процессы дают возможность устанавливать средние рыночные цены и сохранять стабильное качество. Вот вам и клиентоориентированность, и одновременно следование принципу минимального жизнеспособного продукта! Такому подходу, пожалуй, следует поучиться многим другим брендам, даже тем, что не связаны с ножевым делом.
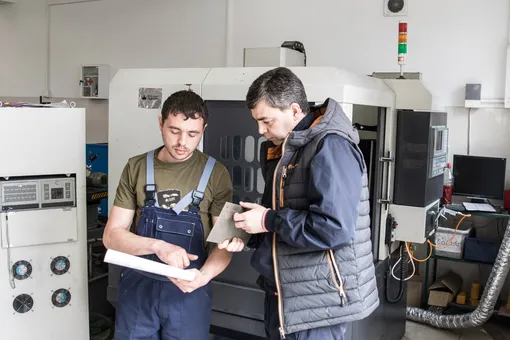
Вырезка по форме — с чистого листа
В основе каждого ножа лежит заготовка, а точнее — стальной лист, из которого по форме вырезаются необработанные изделия. Обычно сплавы для будущих ножей делаются из железа и углерода с добавлением различных примесей, влияющих на свойства стали. Мастера работают как с углеродистой, так и с высоколегированной сталью со сложной химической структурой. Хотя такие материалы труднее поддаются обработке, из них получаются более износостойкие, прочные на излом, устойчивые к сколам и коррозии ножи.

На сегодняшний день завод работает с ножевыми сталями типов 420HC, AUS8, 440C, D2, Niolox, Sleipner, N690, K340, PGK, M390. Это основная линейка, но вскоре Kizlyar Supreme сможет похвастаться еще одной премиальной сталью, поставщиком которой станет Китай.
Первичная обработка
Далее заготовки попадают в следующий цех — первичной грубой обработки. Передавать изделия далеко не нужно: все станки на производстве намеренно расположены близко к друг другу (в одном павильоне или в соседних цехах) — это позволяет сэкономить время на транспортировке.
На этом этапе с помощью станков у ножей формируются вогнутые или прямые спуски, задается толщина по обуху: процесс автоматизирован максимально, операторам остается только контролировать процесс. Затем заготовки попадают в конвейерную закалочную печь с электронным управлением, куда из генератора попадает азот с чистотой не менее 99.95%.
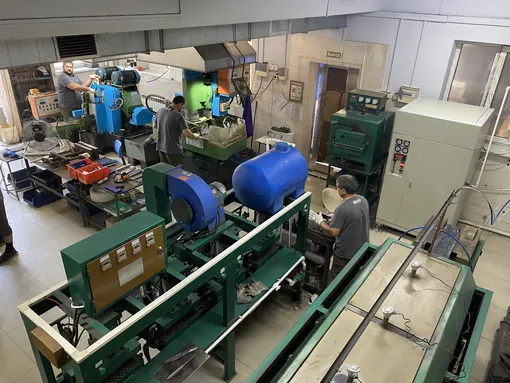
Азот вымещает кислород, поэтому в ходе первичной закалки углерод не выгорает — химический состав металла сохраняется, а верхний слой не чернеет. Так, после второго этапа получаются почти готовые изделия, которые нуждаются в минимальной ручной обработке.
«Грубую обработку некаленых изделий проще производить в самом начале. Если сделать наоборот — сначала закалить, а потом шлифовать, — упадет производительность. Увеличится расход камней, а станки начнут быстрее выходить из строя», - отмечает Виктор Агре.
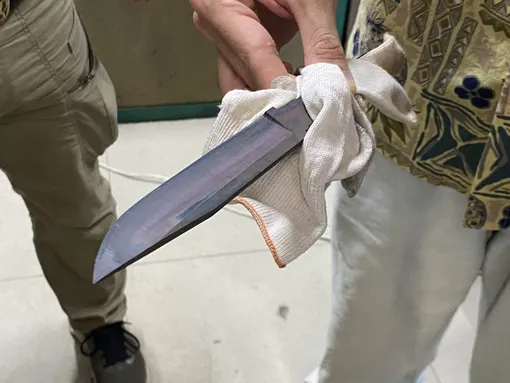
Закаленные ножи становятся слишком твердыми, а потому следующим шагом их нужно отправить на отпуск, чтобы снять напряжение в стали и добиться нужного баланса вязкости. На практике в меру плотный, но гибкий нож будет лучше выдерживать удары. В зависимости от марки стали изделия остывают естественным путем на воздухе или в отпускной печи. Некоторые клинки, особенно из высокотехнологичной порошковой стали, дополнительно проходят криообработку — подвергаются охлаждению при сверхнизких температурах, что дополнительно улучшает структуру стали.
Ручная шлифовка
Полировочный процесс производится с помощью шлифовальных станков. Сидя за ленточными гриндерами, мастера ровняют ножи, убирают зазубрины. В целом — подготавливают изделия к дальнейшей полировке.
«К каждому гриндеру подведена труба: пыль вытягивается через вытяжки, а пылесборники регулярно чистятся. У всех рабочих есть правило — за 15 минут до конца смены проводить уборку. Вообще, все цеха мы стараемся оборудовать так, чтобы там можно было работать без респираторов, только в очках. Хотя защиту мастера все равно надевают», — уточняет Виктор.
Пескоструйная обработка или виброгалтовка
После гриндеров у ножей есть два пути: они попадают либо на пескоструйку, либо на виброгалтовку. За одну только смену подобные аппараты обрабатывают от 1000 до 1500 ножей в день.
Как следует из названия технологии, при пескоструйной полировке в качестве абразивного материала используется песок, который выбрасывается на металл под давлением, обеспечивая глубокую очистку и полировку.
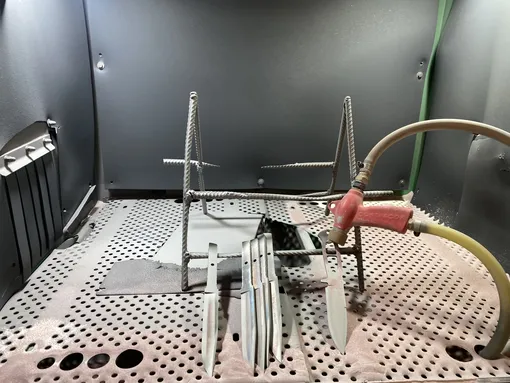
Вибрационные галтовочные машины заполнены не только вспомогательными жидкостями, так называемыми компаундами, но и абразивными материалами разной крупности — пластиковыми шариками, искусственными камнями или керамикой. Перемещаясь из чана в чан, ножи сначала проходят грубую обработку крупными фракциями, а в конце — попадают к мелкодисперсным частицам, доводящим поверхность до блестящего, зеркального финиша.
К слову, далеко не все типы ножей проходят виброполировку. К примеру, клинок компанейро с выпуклой линзой нельзя поддавать такой обработке, иначе скруглятся углы. Для подобной модели будет достаточно аппаратной, а после — легкой ручной отделки.
Фрезерование
Один из самых эффективных с точки зрения производительности — цех с фрезерными станками ЧПУ. Системе задается алгоритм, следуя которому машина вырезает рукоятки для ножей — из дерева, пластика или композитного материала G-10. Готовые ручки покрываются водоотталкивающим составом и подгоняются под клинок.
Сборка и гравировка
На стол к сборщикам клинки попадают незаточенными из соображений безопасности. Рукоятки прикрепляются к отполированным изделиям — все детали вручную собираются в единую конструкцию.
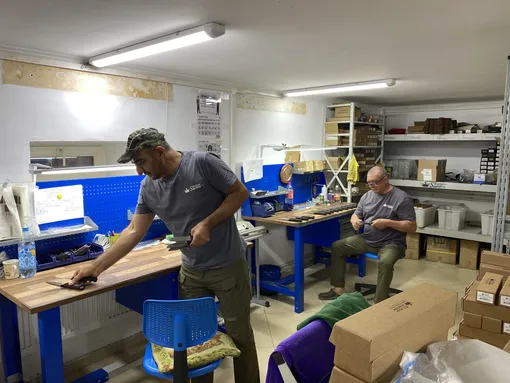
Мы проверили на себе: процесс сборки требует максимальной концентрации и внимательности. А чтобы избежать ошибок, желательно сравнивать каждый собранный экземпляр с эталонной моделью. В завершение на ножи наносят гравировку, соответствующую названию модели.
Заточка и упаковка
Перед упаковкой конечный продукт наконец затачивается, помещается в ножны и собирается в фирменную коробку в комплекте с инструкцией, каталогом и гарантийным талоном. В таком виде все товары, готовые к продаже, отправляются в складские помещения, а после — развозятся по официальным магазинам и дилерским сетям.
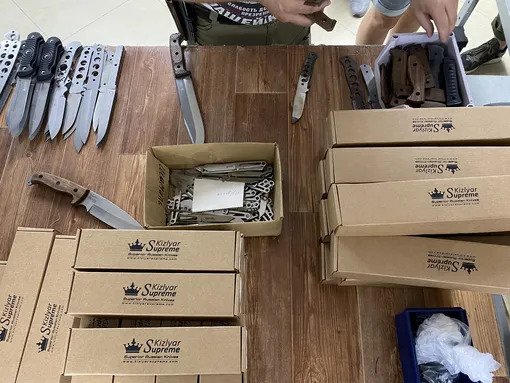
«Не принимай брак, не создавай брак, не передавай брак»: кодекс ножевых мастеров
Сегодня производственная философия Kizlyar Supreme опирается на принципы бережливого производства, так называемого подхода Lean, и систему 5С. Администрация понимает: навязывание сотрудникам этих идей лекциями на общих собраниях не изменит их привычек, а потому просвещение ведется иначе. На входе в каждый цех, на видном месте, висит табличка с советами, позволяющими сократить расходы. Основные рекомендации, конечно, завязаны на чистоте и порядке на рабочих местах. Их мастера видят каждый день, а потому запоминают и соблюдают добровольно — понимают общую выгоду.
Среди других положений, позволяющих исключить потери на рабочем месте, — отсутствие лишних запасов, недопустимость избыточной обработки, сокращение лишних перемещений и введение ворот качества. Первые пункты понятны, а вот последние два стоит пояснить.
За счет небольшой площади мануфактуры и близкого расположения производственных помещений и технического оборудования, сотрудникам нет необходимости долго перемещать изделия между этапами, поэтому готовый продукт получается в разы быстрее. Из-за больших объемов производства заводу приходится рационально использовать любое свободное место: так, недавно, пришлось отказаться от магазина при заводе, чтобы разместить новый цех ЧПУ. Приоритеты расставлены четко. «Расширение оказалось важнее розничных продаж», — признается руководитель завода Елена Пасашникова.
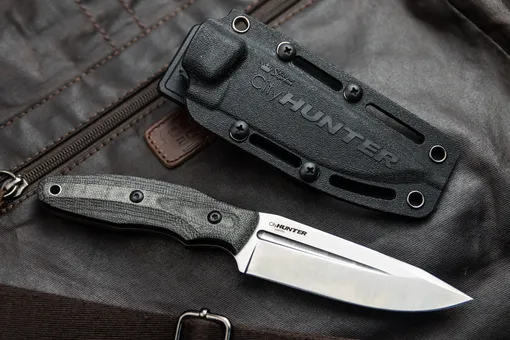
В концепцию Lean-производства входит и постоянный контроль качества товара на каждом этапе. Причем за браком следит вся команда. Любой из сотрудников, сделав брак, сообщит о нем и постарается исправить ошибку. Так же, как если с предыдущего этапа к мастеру попадет изделие ненадлежащего качества, он не пропустит его дальше.
«Мы создаем принципиально другой способ контроля качества. Никто никого не наказывает за брак. Наоборот, чем раньше мы его обнаружим, тем дешевле он нам обойдется», — уверяет Виктор Агре.
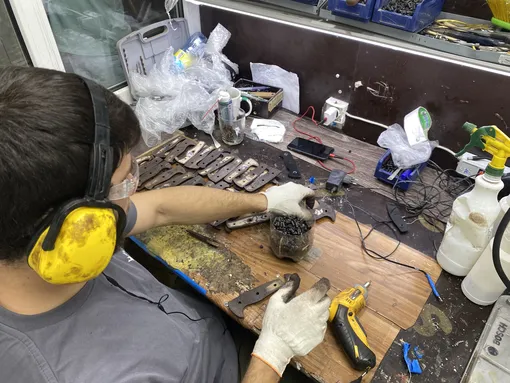
Тренды, которые все больше внедряет в свое производство крупнейший российский производитель ножей, глобально выводят отечественную ножевую индустрию на уровень выше. Если еще совсем недавно мы только догоняли западных коллег, то сейчас, как минимум, стоим с ними на одной ступени, завоевывая признание международной аудитории. Несомненно, кизлярскому производству есть куда расти: в Санкт-Петербурге уже открылась и развивается новая производственная площадка бренда. А со временем, когда искусственный интеллект станет понятнее и доступнее, возможно, часть процессов будет роботизировано, что также позволит заводу нарастить мощности.