Идее Генри Форда строить автомобили в жестком, последовательном порядке уже более века. За это время машины научились самостоятельно переключать передачи, парковаться, двигаться, тормозить, выезжать из «сотни» за считанные секунды, спасать человеческие жизни, запоминать ваши маршруты, предупреждать об опасностях, даже писать посты на Facebook (Социальная сеть признана экстремистской и запрещена на территории Российской Федерации), но конвейерная сборка до сих пор остается каркасом и движущей силой массового производства. Никто из гигантов до этого момента не пытался покуситься на Святой Грааль автомобилестроения, но такие дерзкие инженеры все же нашлись, и работают они в Ингольштадте. «В течение десятилетий это было наилучшей методикой, но теперь она должна быть переосмыслена», — говорит Фабиан Русичка, основатель Arculus, внутреннего проекта Audi.
Умная фабрика: как автомобили собираются без людей
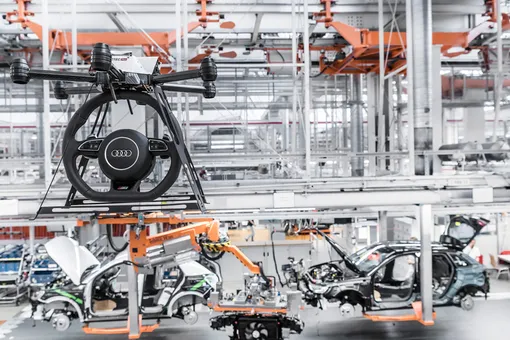
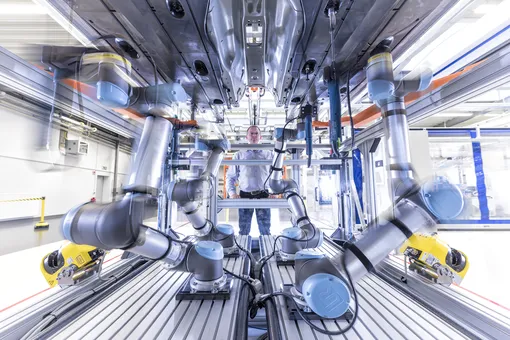
Из мира биологии мы знаем, что arculus (он же аркулюс) — это жёсткий элемент в структуре крыла насекомого, испытывающий постоянные нагрузки, или, если говорить энтомологическим языком, перемычка между жилками MP- и CuA+; без этой детали они не могли бы летать. Разработчики с оптимизмом смотрят в будущее, считая что эволюция автомобилестроения именно за модульной сборкой, поэтому их проект непременно взлетит. Так чем же модульная сборка отличается от конвейерной? И в чем ее основные преимущества?
В Ингольштадте сборочные линии работают на фиксированном интервале в 90 секунд. Это означает, что некоторые из них трудятся вхолостую, к примеру, в процессе установки климат-контроля, который входит не во все комплектации. Чем более индивидуальную, чем более заполненную опциями машину заказывает покупатель, тем больше холостой работы выполняют механизмы на некоторых сборочных этапах. А если вы захотели автомобиль не с ДВС, а электродвигателем? Для этого производитель должен сделать дополнительный блок на конвейерной линии, и он бы тоже простаивал какое-то время.
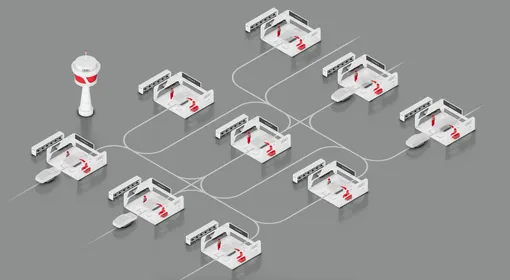
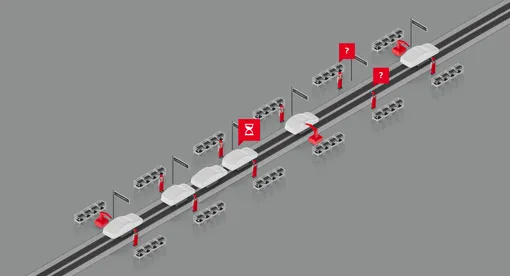
Модульная структура сборки как раз и решает эти проблемы, являясь принципиально новым и гибким инструментом. К примеру, Audi A3, прежде чем быть упакованной и отправленной будущему владельцу, должна пройти порядка 160 этапов сборки, каждый из которых обслуживают не один десяток человек. А при экспериментальной модульной сборке, которая насчитывает примерно 200 независимых станций, контроль осуществляется максимум двумя (!) специалистами завода.
Если на ряд машин надо установить оборудование ограниченной серии, просто ставится дополнительный модуль, куда авто будет доставлено с помощью тележки DTS.
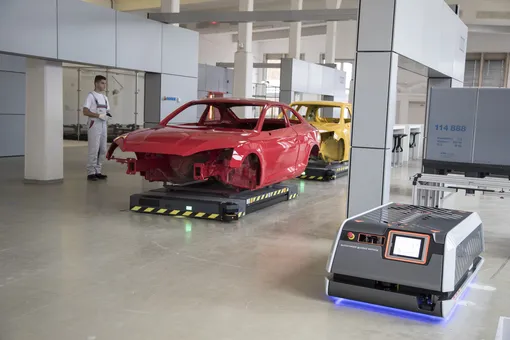
Автономный курьер
DTS — это driverless transport systems, система, которая управляет «роботами-тележками» Audi AGV (автоматически управляемое транспортное средство). Таких AGV существует два вида: одни перевозят машины между модулями, другие — поставляют необходимые запчасти и навесное оборудование к ним же.
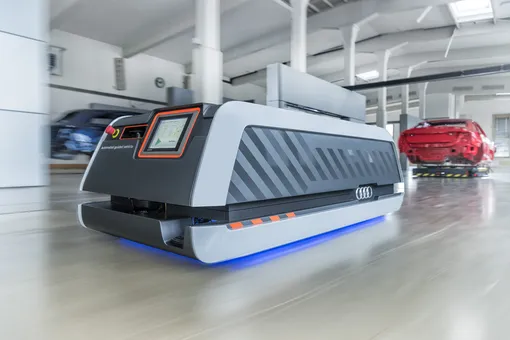
Автономное движение обеспечивается специальными лазерными датчиками, установленными по всей территории завода на высоте 17,5 от пола с рабочим диапазоном в 190 градусов и 49 метров по горизонтали и 17 градусов по вертикали. Погрешность движения по маршруту — не более одного сантиметра.
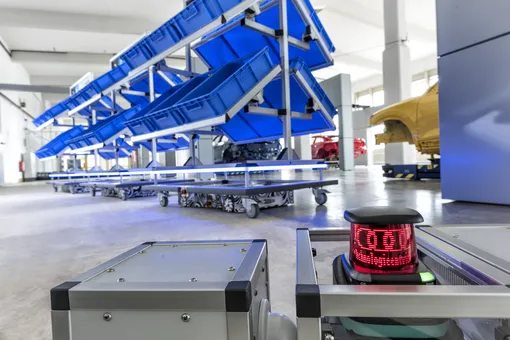
При этом, если перед AGV возникает препятствие, она останавливается и сообщает об этом оператору. Скорость в настоящее время ограничена на 4 км/ч. Если работник использует один и тот же маршрут, что и AGV, тележка остановится поскольку настроена на более низкий приоритет.
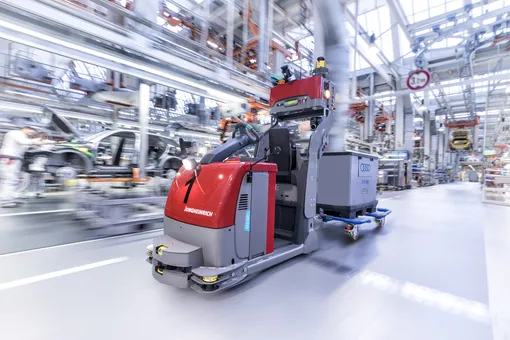
Команда разработчиков, отвечающих за Audi AGV, говорит, что они уже близки с серийному производству по такой схеме. Поэтому в ближайшее время «автономные курьеры» будут трудиться не только на Smart Factory, но и заводах Европы и Мексики.
Детали
В планах Audi автоматизировать не только сборку, но и производство деталей, повысив при этом качество штамповки, за которое, как вы уже догадались, будут отвечать снова роботы. Но для этого надо было разработать новые прессы, которые, как говорят представители компании, основаны на бионических принципах. Они гораздо легче, чем их предшественники, при этом обеспечивают большую жесткость и точность.
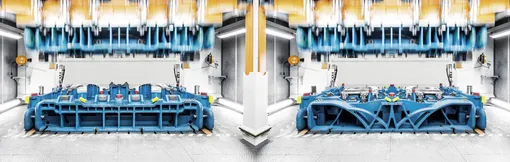
В цехе размером с пять футбольных полей стоит классический пресс (по сути уже история) около пяти метров в длину, трех в ширину и весом в 45 тонн. Его несущая конструкция состоит из массивных балок, расположенных по горизонтали и вертикали — за счёт этого обеспечена его жёсткость и возможность равномерного воздействия на обрабатываемую деталь.
Но он в Ингольштадте лишь для сравнения, поскольку на смену одному такому гиганту приходят малые прессы с закругленными несущими и рабочими поверхностями, выгибающими детали в соответствии с данными, получаемыми от датчиков давления. Благодаря этому сильно повышается точность, допуски при изготовления деталей стремятся практически к нулю, а жесткость системы значительно возрастает, что позволяет обрабатывать более широкий спектр материалов с разными силами. Если с помощью классического пресса декоративное ребро на крыле автомобиля можно сделать, например, шириной 2 см, то «биоморфный» пресс позволяет увеличить точность обработки в несколько раз, причём от машины к машине отклонения будут минимальны. А перед отправкой на сборку параметры всех деталей сканируются роботами.
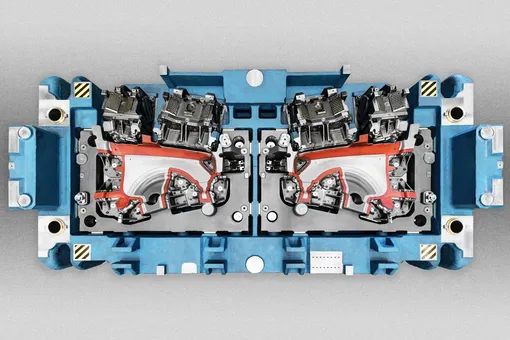
Металлическая 3D печать
Эта методика также известна как селективное лазерное плавление. Основной принцип работы — спекание металлического порошка (размер зерен от 15 до 40 мкм, то есть меньше, чем толщина человеческого волоса).
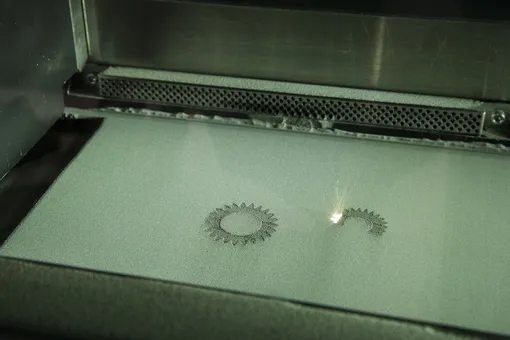
Анализы и тесты показывают, что печатные алюминиевые детали имеют примерно в два раза больший предел прочности на разрыв эквивалентных частей, и к тому же они на 20−30% легче деталей, изготовленных из конструкционного литья.
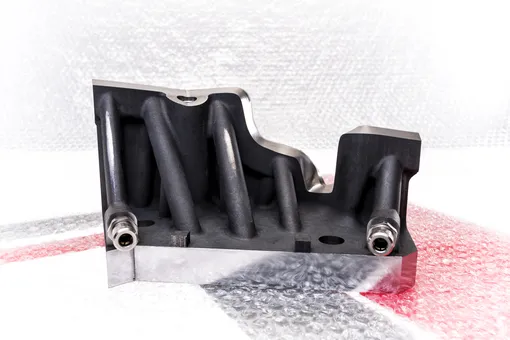
Однако это очень дорогой и медленный процесс, плюс существуют ограничения по размеру (не более 40 см). Поэтому применение данной технологии будет ограничиваться пока только дорогими машинами — Audi R8, а также инновационными проектами, в которых участвует Audi. Например, так сделано колесо для лунного модуля XPRIZE, разработанного Audi совместно с компанией EOS.
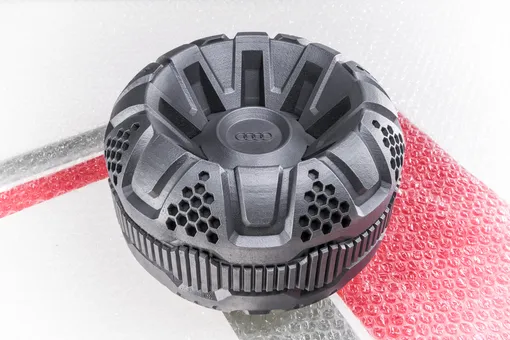
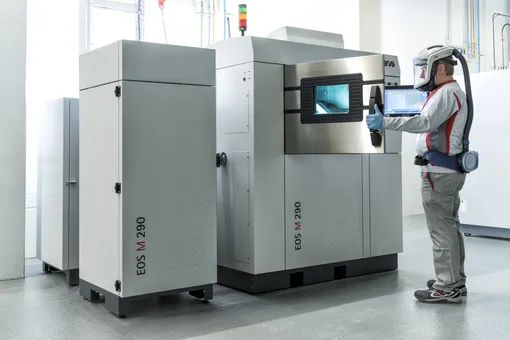
Взгляд робота
И, безусловно, в автомобильную промышленность начал активно проникать ещё один модный и очень активно растущий ныне тренд — виртуальная реальность. Сотрудники Audi Smart Factory с помощью HTV Vive и на примере виртуальной Audi Q2 показывают, как они проверяют компоновку навигационной системы. Воссоздается не только блок, который спрятан под панелью, но даже штифты, чтобы выявить все проблемы на этапе моделирования.
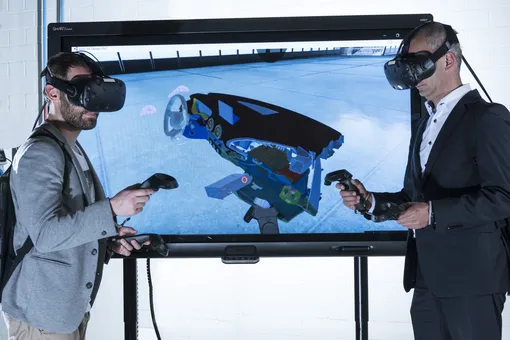
В очередной раз мы приходим к тому, что робототехника с каждым годом будет все больше и больше внедряться в те процессы, которые ранее исполнялись за счет человеческой силы. Основным камнем преткновения является стоимость и скорость, и как только эти две проблемы удастся решить, человек в массовом автомобилестроении будет лишь контролирующим органом. Которого, в свою очередь, контролируют роботы.