С тех давних времен технологии производства сталей с разными свойствами ушли далеко вперед и продолжают совершенствоваться в наши дни. Без серьезного прогресса в металлургии было бы невозможно изобрести многие очень важные и широко распространенные сегодня машины и механизмы, такие, например, как двигатели внутреннего сгорания, трансмиссии, редукторы и т. п. Детали этих устройств, которые должны выдерживать экстремальные механические и температурные нагрузки, изготавливаются из специальных высокопрочных марок стали, технологиями производства которых владеет далеко не каждое металлургическое предприятие.
Секреты современной стали
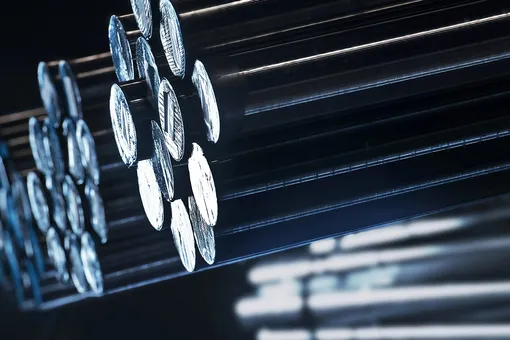
К таким специальным сталям относится в том числе SBQ (Special Bar Quality) — сортовой прокат с повышенными качественными характеристиками. Он используется для изготовления ответственных деталей в автомобилестроении, машиностроении, судостроении, авиастроении и других отраслях. Известно более 500 марок стали особого качества. В России лидером по производству SBQ является Оскольский электрометаллургический комбинат (ОЭМК), входящий в компанию «Металлоинвест».
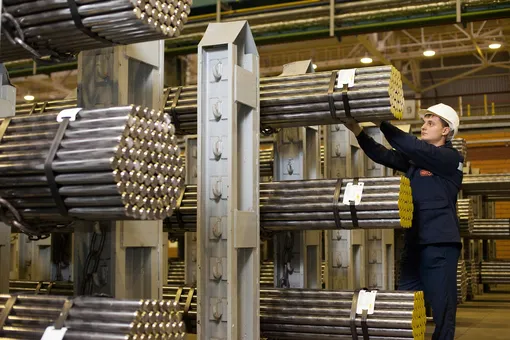
Металл высокой чистоты
Представители этого предприятия рассказали «ПМ», как и для чего производится такая сталь. Чтобы выплавить сталь определенной марки, нужно прежде всего сделать так, чтобы в ней были все полезные примеси и было как можно меньше бесполезных или вредных. Для выплавки стали на ОЭМК используют первородную шихту — металлизованные окатыши, произведенные из высококачественного железорудного сырья Лебединского горно-обогатительного комбината, также входящего в «Металлоинвест». Металлизованные окатыши получают по специальной технологии: путем восстановления железа из руды с помощью нагретого до 800−1000°С природного газа. Они уже содержат в себе довольно мало вредных примесей и являются идеальным сырьем для производства сталей с узким диапазоном химических элементов. Окатыши загружаются непосредственно в электродуговую печь, в которой выплавляется сталь.
Чтобы получить конечный продукт — стальной пруток специального качества, из которого потом будет изготовлен подшипник или другая деталь автомобиля, требуется провести много сложных физико-химических процессов. Из жидкого металла удаляют вредные примеси, прежде всего такие, как сера и фосфор. Для придания высокой прочности и пластичности добавляют так называемые легирующие присадки. Это марганец, кремний, хром, никель, медь. Однако легирование — это еще не все.
Из стали удаляют лишние газы в процессе вакуумирования. Расплав продувают инертными газами для получения равномерного химического состава по всему объему. Важный момент — горячая прокатка стали при точно заданных параметрах температуры. Это позволяет управлять микроструктурой металла, от которой зависят многие свойства конечного продукта. Наконец — обточка и полировка готовых прутков для обеспечения высокого качества поверхности. Это лишь краткое и упрощенное описание того, как создается качественная стальная продукция. На самом деле технологий больше, они очень сложные и требуют современного высокотехнологичного оборудования.
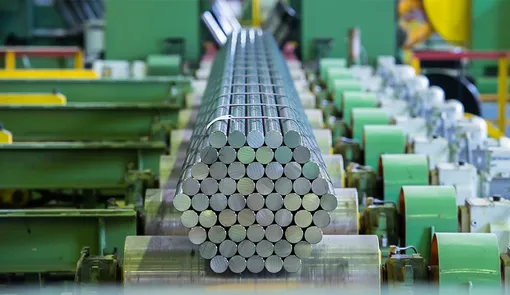
Фантастическая выносливость
SBQ — элитная продукция в мире металлургии. Стали, сделанной на ОЭМК, мы доверяем свои жизнь и безопасность. Где же применяется SBQ?
Одним из партнеров ОЭМК является Уральский пружинный завод — поставщик пружин для производства грузовых вагонов. Представим себе всем известный полувагон (вагон с высокими бортами и открытым верхом). Масса его приблизительно 25 тонн, груз может достигать 300% от этого значения — около 100 тонн. Это на 20 тонн больше максимального взлетного веса Boeing 737. 100-тонные махины движутся в составе огромных поездов, но достаточно, чтобы один вагон сошел с рельсов, и поезд потерпит крушение с непредсказуемыми последствиями.
Чтобы не допустить подобных случаев, особые требования предъявляются к вагонным тележкам. При максимальной нагрузке 50 тонн на каждую тележку, от нее требуется 500 000 км безаварийного пробега. Важной частью вагонной тележки является амортизационная подвеска, в которой ключевую роль играют пружины. На Уральском пружинном заводе их изготавливают из SBQ, произведенного на ОЭМК.
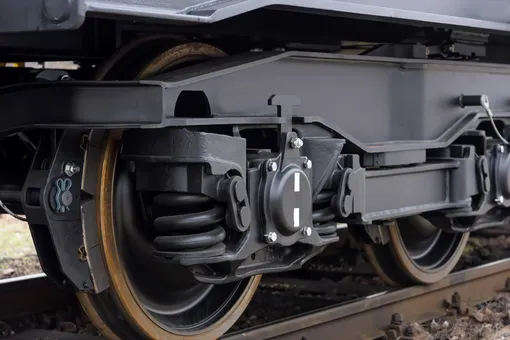
В сердце автомобиля
Высокоточная механика в автомобиле также невозможна без специальных марок стали. Иначе механизм быстро деформируется и разрушится. Коленчатый вал — ключевая деталь в двигателе внутреннего сгорания (ДВС), и от него требуется особая прочность. Имеющий в основе простейший механизм кривошипа, вал подвергается многообразным нагрузкам, в том числе по сути энергии взрывов, происходящих в цилиндрах и передаваемых через поршень и шатун. На коленчатый вал действует и сила инерции, возникающая от возвратно-поступательного движения. К этому можно добавить нагрев и многочисленные вибрации.
Коленчатые валы давно не делают сборными — их выковывают или отливают из цельного куска металла, а затем подвергают дополнительной механической обработке. Разумеется, выбор стали для изготовления вала принципиален — это должен быть прочный и стойкий материал. ОЭМК активно сотрудничает с предприятиями автомобильной промышленности, такими как КАМАЗ, АвтоВАЗ, Renault-Nissan, PSA, Volkswagen, Ford и другие. На КАМАЗе из SBQ, поставленного ОЭМК, изготавливают не только коленчатые и распределительные валы для двигателей, но и детали подвески, а также зубчатые колеса для трансмиссии и других редукторных узлов, где важна субмиллиметровая точность и неприемлема деформация.
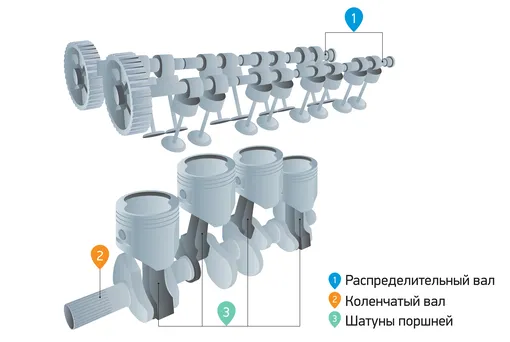
Андрей Сергеевич Савинков, заместитель главного конструктора ПАО «КАМАЗ»: «Основные цели автопроизводителей в условиях высокой конкуренции на внутреннем и внешнем рынках сбыта — это снижение материалоемкости. Из практики эксплуатации грузовых автомобилей известно, что снижение этого параметра на каждые 500 кг приводит к увеличению грузоподъемности и уменьшению расхода топлива до 0,4 л/100 км, а также к уменьшению вредных выбросов в окружающую среду.
Вместе с тем мы понимаем, что уменьшение материалоемкости не должно приводить к ухудшению других потребительских свойств — прочности, долговечности и ресурса машин. Ключевым изделием грузового автомобиля, его своеобразным «становым хребтом» является рама, к которой крепятся все остальные элементы: кабина, грузовая платформа, силовой агрегат и другие автокомпоненты. Причем рама должна быть и жесткой, и прочной, и упругой в различных направлениях одновременно. Кроме этого, она должна сопротивляться кручению вокруг продольной оси.
Поэтому весьма заманчивой является идея применения высокопрочных сталей с улучшенными прочностными характеристиками. Основной такой характеристикой является предел текучести: для обычных сталей марки 20ГЮТ он составляет 490–550 МПа, для высокопрочных типа S600MC — 600–700 МПа».
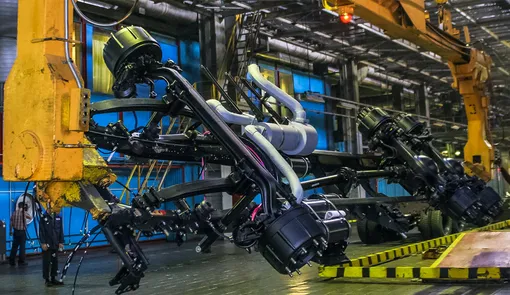