Наш разговор о 3D-печати мы начнем с истории, которая случилась больше ста лет назад. В цех Путиловского завода, который в начале XX века занимался производством паровых котлов для огромных военных кораблей, пришли инженеры. Они принесли новую модель котла. Мастер посмотрел на чертежи, покачал головой и сказал: «Один котел я сделаю, а второй не смогу». «Почему?» — изумились разработчики. Мастер показал на чертежи: «Здесь нужно заклепки ставить изнутри. Есть у меня один лодырь, я его в котле и оставлю. А больше таких лодырей у меня нет». И инженеры пошли думать, как бы так сделать новый котел, чтобы не пришлось никого оставлять внутри.
3D-печать в России сегодня и завтра
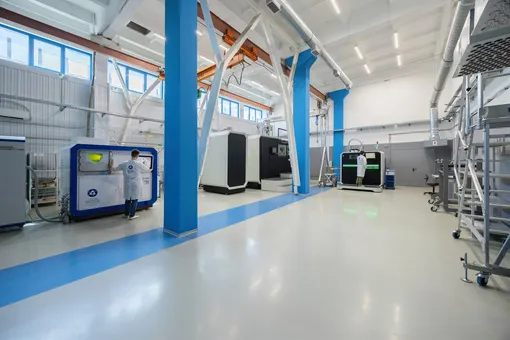
А вот если бы у инженеров был 3D-принтер нужных размеров, таких трудностей не возникло бы.
Основные идеи 3D-печати были запатентованы в 1980-х – начале 1990-х годов, хотя назывались они тогда по-другому. Но в то время они не нашли сколько-нибудь значимого применения. Возможно, просто потому, что были очень дороги, и использовать их могли только крупные корпорации, но они их не очень интересовали. Но идеи трехмерной печати были сформулированы. И начали развиваться.
Аддитивное производство
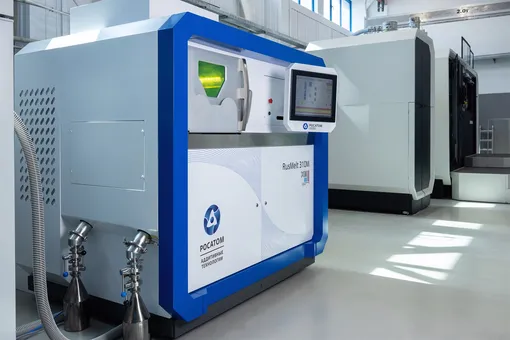
3D-принтеры — это устройства так называемого аддитивного производства, в котором процесс создания продукта противоположен традиционному — субтрактивному. Как обычно производится потребительский товар или деталь механизма? Так же, как скульптор создает свое творение: берется заготовка, например, кусок мрамора или стальная проволока, отсекается лишнее и получается продукт: статуя Давида или крестовая отвертка. При этом все, что мы отсекаем, летит в отходы.
Но можно поступать иначе: мысленно рассечь продукт, который мы только собираемся сделать, на тончайшие слои и, нанося слой на слой, постепенно «вырастить» готовое изделие. Это и есть аддитивное производство. Отходов в этом случае практически нет, форму можно придумать самую прихотливую — наша фантазия ограничена только законами физики и свойствами материалов. Это и делает 3D-принтер.
Виды 3D-печати
Устройства 3D-печати бывают разных конструкций и по-разному формируют слои объекта. У 3D-принтера есть печатающая головка (или несколько таких головок) и рабочая платформа. Передвижением головки и платформы и подачей материала управляет компьютер, использующий специальную программу — описание 3D-модели. Иногда материал подается прямо через головку (у принтеров типа FDM), иногда прямо на стол, например, если применяется трехмерное ламинирование (Laminated Object Manufacturing).
При стереолитографировании (устройства типа SLA) материал — жидкий. Он наливается на стол, а потом засвечивается лазером или ультрафиолетом. При засвечивании жидкость твердеет, и можно заливать следующий слой. При лазерном спекании или сплавлении (Selective Laser Sintering — SLS, Selective Laser Melting — SLM, Direct Metal Laser Sintering — DMLS) на платформе рассыпается специальный порошок. Под действием лазера частички схватываются и образуют нужный узор, а потом рассыпается новый слой порошка, и действие повторяется. При технологии DMLS в качестве порошка берется металл (если это титан, то рабочий стол погружается в вакуум, чтобы металл не окислялся) и нужный узор образуется под воздействием лазера, расплавляющего/спекающего порошок. Так слой за слой строится продукт.
Без швов и заготовок
У 3D-печати много преимуществ. Если мы создаем сложное устройство, например, турбину или двигатель, традиционными методами, мы сначала делаем небольшие детали, а потом из них собираем готовый продукт. Но, как говорится в одном из законов Мэрфи, «все швы текут». Это, конечно, шутка, но в действительно при высоких нагрузках швы и соединения являются самым уязвимым местом любой конструкции. 3D-печать позволяет избежать этой проблемы: в продукте просто нет швов, он весь состоит из одного куска.
Приведем пример. Ученые Уральского федерального университета предложили использовать 3D-печать при создании изделий для авиационно-космической техники. Доцент университета, соавтор работы Степан Степанов объясняет преимущества 3D-печати так: «При 3D-печати снижается вес изделия без потери надежности. При традиционной сборке, как бы мы ни старались, "лишние" конструкции, которые нужны при сборке, но не нужны при работе изделия, почти всегда остаются. 3D-печать позволяет этого избежать».
Степанов так описывает традиционный процесс: «Сегодня умеют создавать детали из алюминидов титана, но традиционными технологиями из деформированных полуфабрикатов, прутков и так далее. Стандартная технология включает несколько этапов: получение заготовки, механическая обработка, термическая обработка; и она не очень экономична».
Когда мы работаем с 3D-печатью, нам не нужно заранее готовить детали, а потом собирать их. Все, что нужно, сделает сам принтер. Фактически все изготовление очень сложной установки состоит из одного шага — самой печати, то есть, процесса лазерного сплавления металлического порошка.
Настоящее и будущее 3D-печати в России
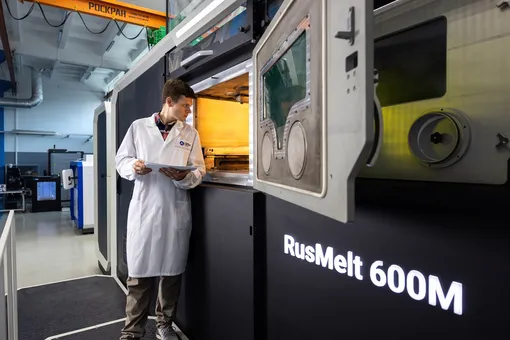
Сегодня отношение к развитию 3D-печати и аддитивному производству в России самое серьезное. Мы рассказали о работе ученых Уральского федерального университета (ее поддержал Российский научный фонд), но это, конечно, далеко не все, что делается в этом направлении.
Одним из лидеров направления 3D-печати в России является госкорпорация Росатом. Бизнес-направление «Аддитивные технологии» Топливного дивизиона Росатома уже запустили серийное производство отечественного 3D-принтера RusMelt 310M. Компания также производит расходные материалы, из которых 3D-принтеры создают изделия и товары; в первую очередь, это металлические порошки для лазерного сплавления.
Компания занимается просвещением и обучением в области 3D. Для этого разворачиваются в сотрудничестве с российскими университетами Центры аддитивных технологий общего доступа. Также была открыта специализированная лаборатория в образовательном центре «Сириус» в Сочи. На базе этих центров можно пройти обучение и всерьез погрузиться в вопросы 3D-печати. А чтобы увидеть и понять, что же сегодня делается на самом переднем краю, стоит заглянуть на ВДНХ: там 12–13 ноября пройдет главная конференция по 3D-печати в России VI «Лидер-Форум».
Все по размеру
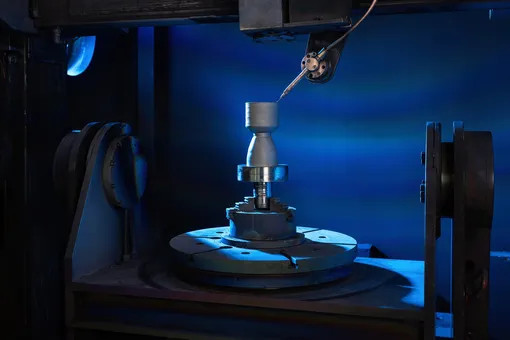
Еще одним преимуществом аддитивных технологий является максимально возможная персонализация продукта. Когда вы открываете каталог товаров известной фирмы, вы видите фотографии готовых изделий. То есть, сапожки надо сначала стачать, потом надеть на ногу и только после этого сфотографировать. Это довольно непросто. А понравится ли кому-то этот фасон — неизвестно.
3D-принтер в качестве исходного образа использует специальный файл 3D-модели. Это может быть полученный 3D-сканированием образец реальных сапожек. Но это может быть и образец, который никогда не воплощался в реальности. И таких чисто виртуальных образцов может существовать не просто больше, чем реальных, — а неограниченно много. И потребитель не только выбирает себе из этого бесконечного набора сапожки по душе, но и сообщает дизайнеру (который здесь же рядом онлайн), что надо такие же, но с перламутровыми пуговицами. И тут же получает образец с перламутровыми пуговицами.
Если у потребителя есть 3D-скан стопы (что легко сделать, да и просто необходимо при таких покупках), он пересылает образец и скан в находящуюся по соседству небольшую компанию, у которой есть 3D-принтер, а потом, когда ему будет удобно, забирает готовые сапожки, сделанные в полном соответствии с его анатомическими особенностями анатомии стопы и вкусовыми предпочтениями. При этом не нужен склад для хранения готовой продукции и вообще не нужна готовая продукция в количестве более одного экземпляра.
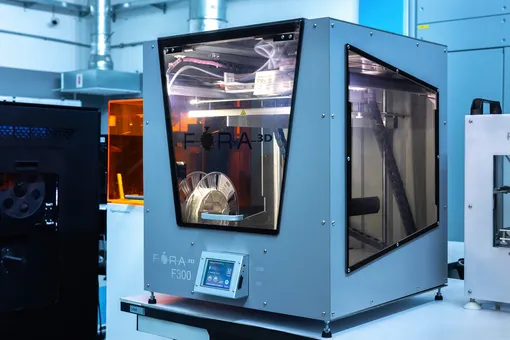
Конечно, сапожки не обязательно делать точь-точь по ноге клиента. Но есть изделия, в которых даже микронное отклонение критично. Для их изготовления используются медицинские 3D-принтеры. С помощью 3D-печати уже изготовлены сотни тысяч чашечек для тазобедренных костей. Такие чашечки нельзя изготовить серийно, поскольку нужны индивидуальные размеры, но без них человек просто не сможет ходить. Это уже серьезное производство. Аналогичная точность нужна при печати других имплантов, в частности, нижней челюсти и костей черепа.
Есть и такое направление в 3D-печати, как «печать» органов с помощью специального биопринтера из клеточного материала пациента. Пока изготовление «запасных частей» для человека находится в стадии эксперимента, но это как раз тот случай, когда важность задачи трудно переоценить, и потому работа будет продолжаться. Здесь в принципе возможна только максимальная персонализация. Другой размер, другая форма, другой материал не подходят. И потому не страшно, что печать медленная, — подождем.
XX век был веком «готового платья» и стандартных производственных линий. Но люди разные и вкусы у них разные, а производственные линии требуют гораздо большей точности и специализации. Поэтому у 3D-печати большое будущее.