А чтобы понять, как именно, «ПМ» посетила производственную площадку завода «Диамант», разместившуюся в поселке Красное-на-Волге — одном из главных ювелирных центров России. Почему сосредоточение производства колец, сережек и колье случилось именно в этом населенном пункте в 34 км от Костромы, никто точно не знает. Драгоценные металлы здесь не добывают, камни не гранят, но еще
Как делают ювелирные изделия: большой репортаж
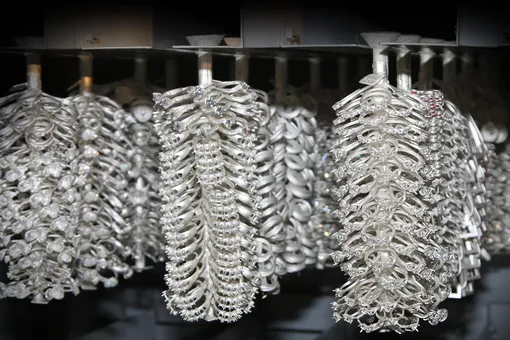
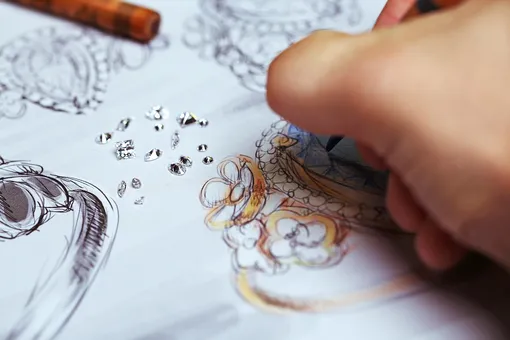
Красиво? Технологично?
Поэтому, конечно, все начинается с замысла художника-ювелира, который и рисует эскиз будущего украшения. «Правда, художник обязан быть немного технологом, — рассказывает Олег Штыркунов, технолог предприятия, любезно согласившийся быть нашим гидом, — ведь то, что красиво смотрится на бумаге, не всегда может быть реализовано в производстве. Мы, конечно, делаем все, чтобы соединить мысль художника с технологическими возможностями, но порой это не удается».
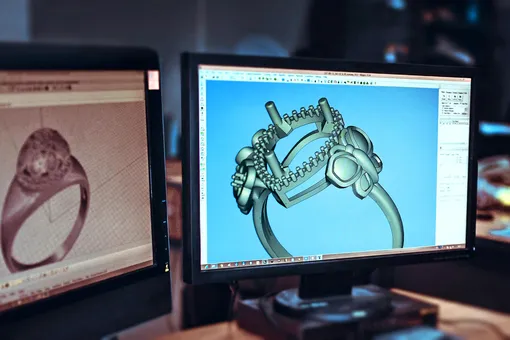
Поэтому одним из ключевых моментов в реализации замысла художника становится 3D-моделирование будущего изделия — именно на этом этапе художественный замысел совмещается с требованиями производственников и службы сбыта. 3D-модельер задает точные размеры посадочных мест для камней, причем допуски здесь составляют порядка 10 мкм, иначе камень либо невозможно будет вставить, либо он легко вылетит из украшения. По окончании всех согласований 3D-модель отправляется на прототипирование.
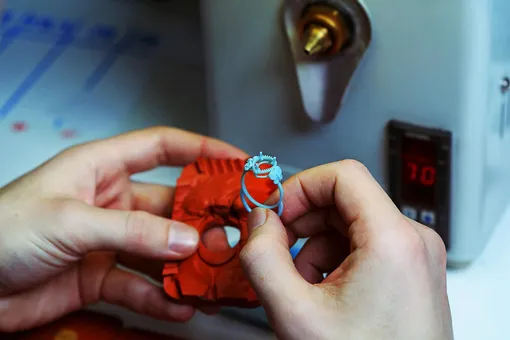
Прототипирование — это распечатка модели на 3D-принтере, причем используются две технологии. Первая — печать пластиком, при которой отдельные «пиксели» на слое жидкой массы отверждаются точечным УФ-излучением. Вторая больше похожа на традиционную струйную печать: головка слой за слоем покрывает поверхность крошечными капельками воска, причем более тугоплавкий синий воск используется для создания собственно промодели, а белый — для поддержки (позже он будет выплавлен). Оба метода имеют свои недостатки: воск дает менее качественные поверхности (их можно подкорректировать вручную специальным инструментом), а пластик всем хорош, но...
Промодели заливают формомассой на основе гипса, чтобы создать формы для литья из серебра. Это будет, конечно, еще не ювелирное изделие, а лишь промежуточная модель. Так вот, при изготовлении форм воск легко плавится и вытекает, а пластик частично горит и оставляет золу, что может в конечном итоге привести к браку литья. И все-таки при моделировании изделий с более тонкими деталями предпочтение отдается пластику.
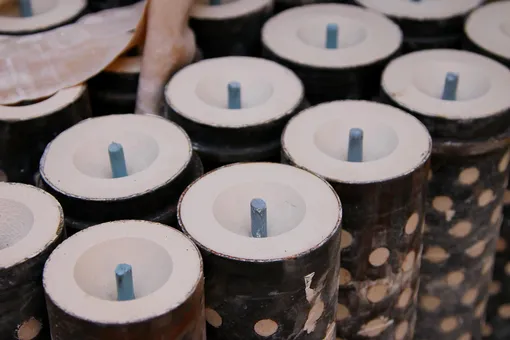
Руки незаменимы
То, что получится из серебра, — еще довольно грубое изделие. Оно несет на себе следы грубой дискретности 3D-печати, и следы эти придется убирать вручную. «Вообще мне хотелось бы подчеркнуть, что при всех индустриальных масштабах производства ювелирных изделий, — говорит Олег Штыркунов, — роль ручного труда, в том числе высококвалифицированного, в производстве по-прежнему велика». Помимо исправления поверхностей, тщательной обработки и корректировки требуют посадочные места для камней — с учетом усадки при литье, усадки восковой, усадки металла. Камень не должен вывалиться или треснуть. Обработка посадочных мест доверяется самым опытным мастерам, так как в конечном счете именно от них зависит качество будущего изделия.
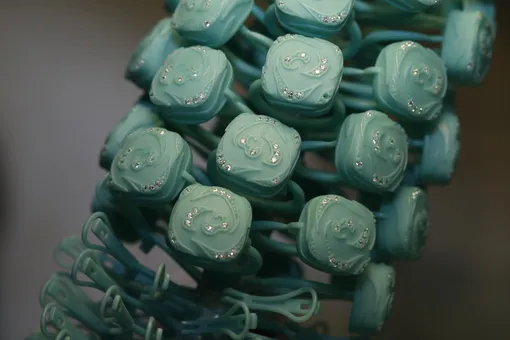
Когда серебряная модель готова, ее помещают внутрь пачки пластин из сырой резины. Мягкая резина плотно облегает металл, повторяя его рельеф. Резиновый брикет отправляется в вулканизатор, подвергается там воздействию высокого давления и температур и возвращается обратно уже в виде довольно твердого монолитного кирпичика. Теперь задача состоит в том, чтобы не просто извлечь из формы серебряную модель, но и очень грамотно, по определенному алгоритму вскрыть форму, превратив ее в две хорошо смыкаемые друг с другом половинки. Необходимо обработать ее так, чтобы добиться хорошей проливаемости металла и вместе с тем избежать появления большого количества облоя.
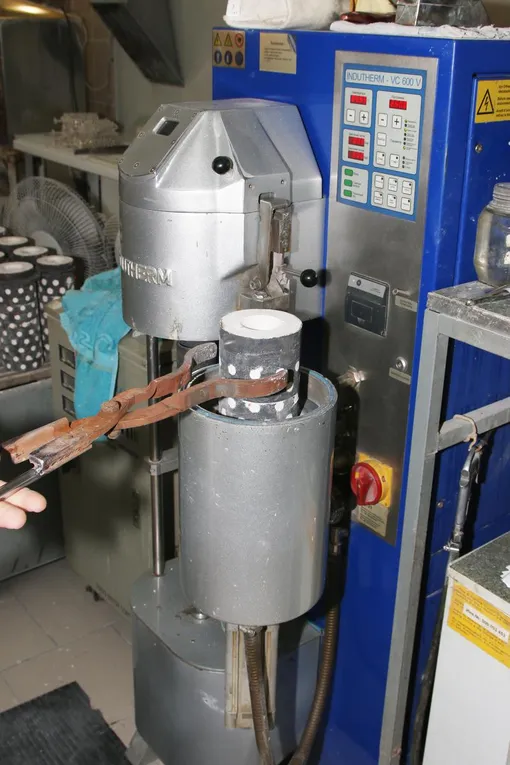
В этих формах будут отливать кольца, элементы сережек и колье, кулоны? Да нет, конечно. Всего лишь очередную промежуточную модель. Но уже каждая такая модель станет прототипом для одного-единственного изделия. Модели делают из литьевого воска с помощью специальных инжекторов. Нагретый воск под давлением впрыскивают в форму, причем эта операция может проводиться как в ручном режиме, так и на полуавтоматических линиях, если требуются особо точные параметры давления и объема воска. Конечно, одна резиновая матрица используется для отливки множества моделей, однако их количество зависит от сложности изделия. Сложные матрицы служат всего пару недель, зато резиновые формы для более простых изделий могут работать годами.
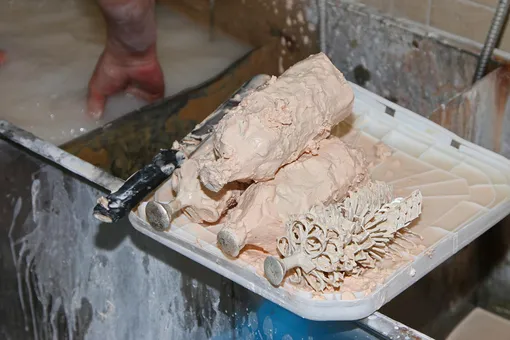
Пустота вместо «елочки»
Разумеется, выплавленные из воска модели подлежат дополнительной ручной обработке — удаляется облой, корректируются поверхности. А затем наступает самый, пожалуй, феерический этап массового производства литых ювелирных изделий. На специальном участке девушки с помощью прибора, напоминающего аппарат для выжигания по дереву, припаивают модели к толстому восковому стержню. Получается то, что производственники называют «елочкой» — и действительно, стержень в окружении «веточек» из моделей сильно напоминает украшенное новогоднее дерево. Стержень втыкается в основание из пластика, что еще более усиливает сходство. Количество веточек разнится в зависимости от размеров будущих изделий — их может быть от десяти до многих десятков.
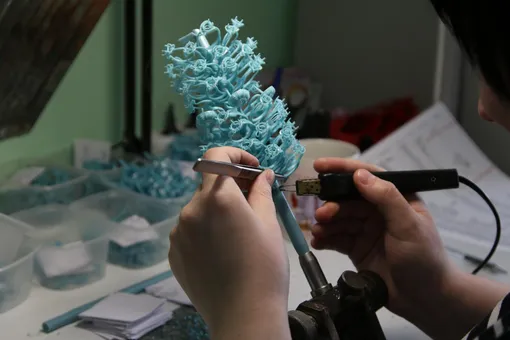
«Елочку» взвешивают и с помощью пропорции рассчитывают количество требуемого драгоценного металла — чтобы не было перелива или недолива. Затем «елочку» помещают в цилиндрическую кассету — опоку — и заливают формомассой, опять же на основе гипса. Тут стоит заметить, что, если в литое изделие предполагается вставить много мелких камней, применяется технология воскового литья с камнями: в опоку погружают «елочку», в восковые элементы которой уже вставлены камешки.
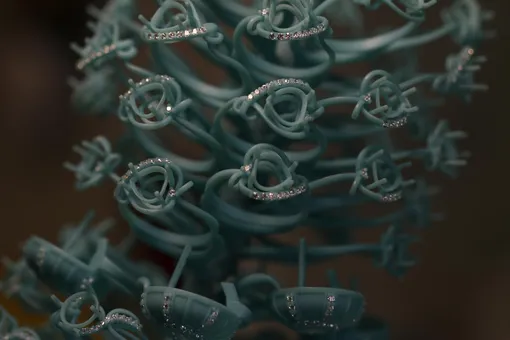
Так делают для того, чтобы впоследствии камни оказались фактически вплавленными в поверхность изделия — создание для них механических креплений-крапанов не дало бы нужной прочности, и появился бы риск выпадения камней. Опоку помещают в печь и в течение нескольких часов подвергают нагреву (обычно в ночные часы). В это время происходит два процесса: формомасса отверждается, а воск вытекает из занятых им полостей через отверстие в основании. Подобно тому как в застывшей лаве Помпей обнаруживали пустоты, образованные сгоревшими дотла телами людей, здесь мы обнаружим пустоту на месте восковой «елочки».
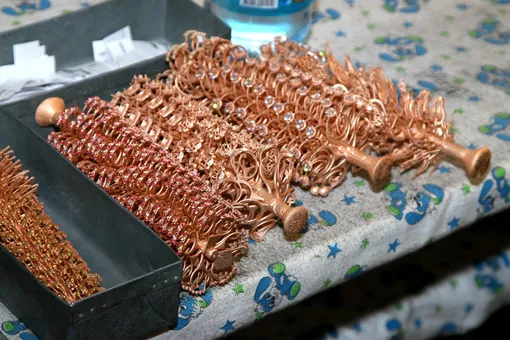
Наконец-то золото!
Следующий этап — печь вакуумного литья. В расположенном в верхней части печи тигле плавится золото или серебро, но до поры до времени он закрыт специальным штоком. Вынутая из печи опока помещается в так называемый стакан под тиглем. Из стакана откачивается воздух, шток вынимается, и под действием силы тяжести и разряжения металл буквально всасывается внутрь формы.
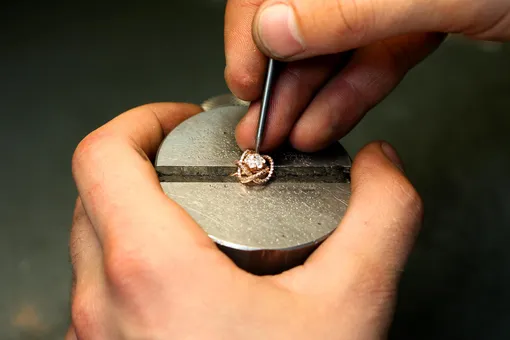
Процесс литья закончен. Если внутри опоки уже есть камни, ей надо дать остыть: мгновенное охлаждение приведет к растрескиванию камней. Если камней нет — можно охлаждать быстро. А дальше совершается нечто прозаическое и волшебное одновременно. Сначала опоку просто помещают под кран с водой, и внешняя часть формомассы быстро размывается и удаляется. Далее в специальной камере остатки формомассы вымываются с помощью находящейся под высоким давлением водяной струи. И мы снова видим «елочку», только теперь она состоит из золота или серебра! Но скоро ей конец.
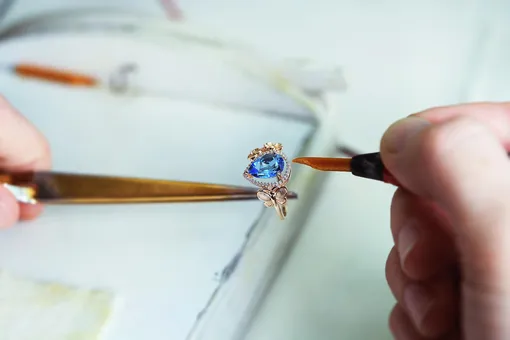
Уже отлитые украшения или их части срезаются с «елочки» специальными ножницами. Заодно удаляются так называемые питатели — технологические элементы, фактически являющиеся слепками каналов, по которым металл (а ранее воск) поступал к отливаемому украшению. Места их сочленений с изделиями заполировываются.
Драгоценная пыль
Конечно, литые украшения, вынутые из печи, еще не имеют того товарного вида, который мы привыкли видеть в ювелирных магазинах. Им необходимо несколько стадий галтовки, то есть шлифовки и полировки в барабанах, наполненных абразивами. Барабаны бывают мокрыми (они наряду с абразивом заполнены жидкостью) и сухими — там жидкости уже нет. Абразивы имеют разную форму и назначение: это могут быть конусообразные гранулы из пластика или молотая кожура грецкого ореха.
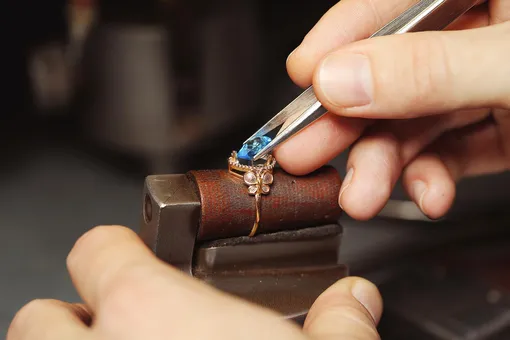
Но все же окончательный блеск украшения приобретают на этапе ручной финишной отделки, где золотые и серебряные поверхности полируют различными инструментами с мягким ворсом. У рабочих в этом цеху руки покрыты слоем металлической пыли, и когда в конце рабочего дня сотрудники моют руки, стекающая вода не уходит в канализацию, а собирается в особых баках, где потом отстаивается.
Затем из осадка экстрагируются попавшие туда частички драгметаллов. «Утилизации отходов драгметаллов, — говорит Олег Штыркунов, — важная часть производственного процесса. С определенной регулярностью на "Диаманте" проводится общая чистка всех поверхностей в производственных цехах с целью сбора ценных отходов. На крупных ювелирных предприятиях на Западе сейчас даже применяют специальные устройства, которые фильтруют воздух в вентиляции, дабы драгметаллы не улетали "в трубу", и, возможно, о такой системе вскоре придется задуматься и нам».