Дальше начинается нечто похожее на старинную детскую игру в «секрет»: это когда надо было аккуратно разгрести землю или песок, чтобы откопать стеклышко, под которым загодя спрятано что-то красивое — бусинки, яркие пуговицы или конфетные фантики. Белое поле — это не бумага, а довольно приличный толщины слой порошка. Теперь надо найти и «выкопать» из него напечатанную 3D-модель. В порошок погружается патрубок от гибкого шланга, и рабочее поле начинает постепенно расчищаться — белая «мука» резво исчезает в недрах невидимого пылесоса. Искомое находится где-то в правом дальнем углу рабочего поля, и этот участок приходится расчищать бережно и аккуратно. Вот оно! Из-под толщи порошка извлекается твердый трехмерный объект — со сложным рельефом, покрашенный в разные цвета, с градиентными заливками. По соседству находится специальная камера. Здесь с помощью сжатого воздуха (применяется инструмент с тонким соплом) все полости модели освобождаются от порошка, причем за счет «мягкого вакуума», создаваемого в камере, клубы этого мелкодисперсного вещества не разлетаются, а мгновенно всасываются куда-то внутрь машины. Именно так — как говорится, «без шума и пыли» — работает 3D-принтер марки Z-Printer 650. Посмотреть на эту пока еще не очень привычную нам машину «ПМ» пригласили в офис эксплуатирующей аппарат московской компании Cybercom. В качестве гидов выступили представитель этой компании Дмитрий Чернобельский и продакт-менеджер компании Consistent Software Distribution Алла Аспидова. Им и первый вопрос: что может и зачем нужна такая весьма дорогостоящая машина?
Назад из виртуальности: модель
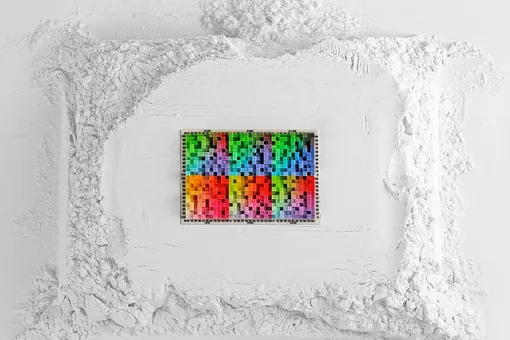
Раскопки в белом порошке
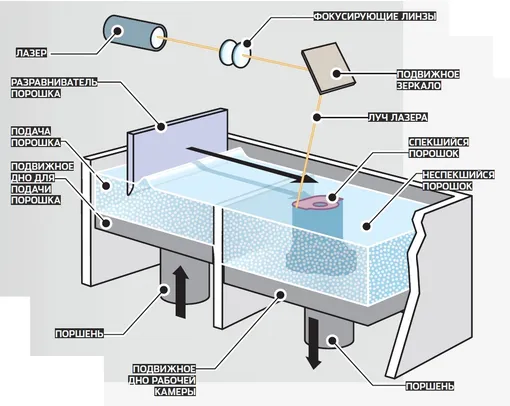
«Основная сфера применения подобных принтеров — прототипирование для САПР, архитектуры, музейного дела, геологии, — говорит Алла Аспидова. — Это разного рода визуализация, которая позволяет максимально реалистично представить себе созданную в недрах компьютера модель. Вот очень простой пример применения этой технологии в экономике. Владимирский стеклотарный завод использует принтер для распечатки моделей стеклотары самого разного дизайна. Раньше, чтобы наладить новую производственную линию разлива и оценить разработанный дизайн, приходилось заказывать индивидуальные стеклянные прототипы стеклодувам, что долго и дорого. Теперь дизайн разрабатывается в САПР и распечатывается. Физическая модель, пусть она и не имеет прозрачности стекла, выглядит все равно реалистичнее изображения на экране. К тому же наша технология трехмерной печати позволяет наносить на модели цветные изображения, надписи, комментарии. Еще интересный пример: одна из английских обувных компаний обязательно делает цветную 3D-распечатку всех своих новых, созданных дизайнерами на компьютере моделей. Конечно, твердые и негнущиеся туфли и ботинки носить нельзя, но в остальном с виду они малоотличимы от настоящих».

Чернила и клей
Принтер, с которым нас познакомили, работает по технологии так называемой холодной печати — в процессе изготовления модели ничего не плавится и не спекается. Специальное программное обеспечение «нарезает» компьютерную CAD-модель на слои толщиной 0,1 мм. Затем модель «выращивается» в рабочей камере принтера путем добавления слоя за слоем (такой метод называется аддитивным). Происходит это так. Над слоем порошка (это композитная смесь на основе гипса) движутся пять печатающих головок - четыре из них содержат цветные чернила и формируют цветное изображение из красок модели CMYK. Пятая головка дает прозрачный цвет. Но, разумеется, цвет — это не главное. Вместе с цветными чернилами, точно по контуру заданного компьютером слоя, на порошок разбрызгивается клей. В итоге обработанный клеем порошок затвердевает и превращается в твердую пластину, поверх которой вновь насыпается порошок — он тут же прилипает к уже созданной части модели. Затем новый порошок вновь обрабатывается клеем и, если нужно, окрашивается. Так появляется следующий слой. Модель постепенно растет вверх — со скоростью 28 мм/ч.
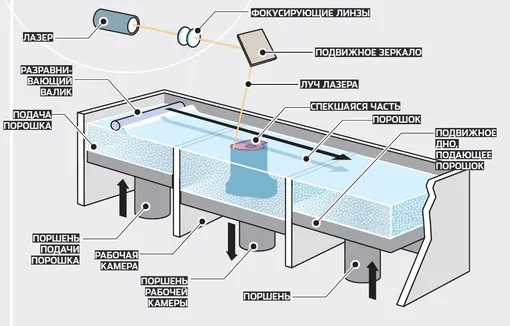
«Технология трехмерного прототипирования, кстати, применима и в медицине, - рассказывает Дмитрий Чернобельский. — В одной из московских клиник такой принтер используют для изготовления прототипов сложных зубных протезов. Сначала челюсть пациента сканируют томографом, затем полученные данные загружают в трехмерный редактор, где проектируют протез. После изготовления на принтере его физической модели работа по протезированию уже идет гораздо проще и занимает меньше времени. Риск ошибки минимизируется». «Принтер можно применять и в более сложных случаях, — добавляет Алла Аспидова. - Например, если после серьезной травмы черепа на него предстоит поставить накладку из титана, проще и быстрее отсканировать череп томографом, создать его физическую модель (включая модель пораженной зоны) и уже на ней проектировать металлическую вставку. Так срок подготовки к серьезной операции может сократиться с нескольких дней до нескольких часов. Впрочем, сегодня существуют 3D-принтеры, способные печатать из медицинских материалов и создавать не прототипы, а непосредственно протезы, например фрагменты разрушенной кости».
Как напечатать механизм
Среди образцов, напечатанных на Z-Printer, неизменно привлекают внимание модели с движущимися частями. Это, например, модель подвески автомобиля, подшипник или демонстрационный механизм с несколькими сцепленными друг с другом зубчатыми колесами (на фото). Достаточно покрутить одно колесо, и в движение придут все остальные. Невозможно даже представить себе, что все это не собрано из отдельных деталей, а напечатано как единое целое.
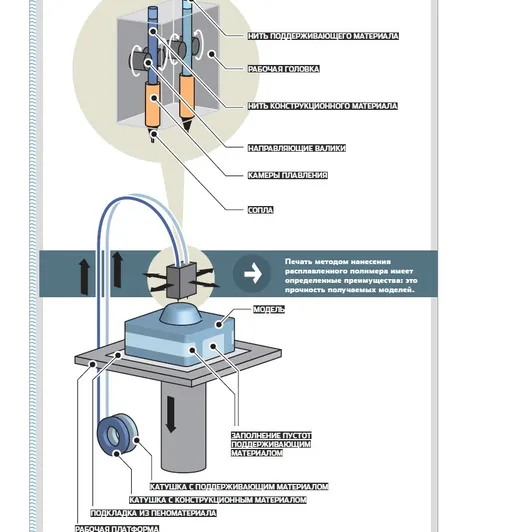
«Чтобы модель двигалась, нужен всего лишь маленький зазор между частями, — объясняет Алла Аспидова. - Этот зазор (минимум 0,1 мм) уже заложен в 3D-модель, и принтер, когда печатает, оставляет непроклеенный участок между движущимися частями. За счет такой технологии можно делать детали, которые другими методами изготовить очень трудно, например подшипники без сепаратора. Причем это очень дешевая технология, так как изделие в процессе печати находится в массе порошка, который заполняет зазоры и не дает модели просесть под собственным весом. В других технологиях приходится использовать для аналогичных целей специальный материл поддержки, который может быть весьма дорог. Кроме того, в процесс изготовления детали привносится еще один этап — необходимость удаления поддерживающего материала из готовой модели методом растворения или выплавления».
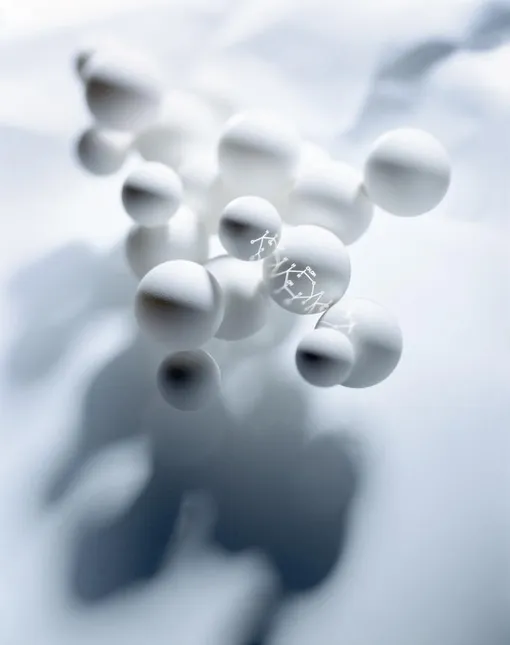
Модели, напечатанные на основе гипсового порошка, шероховатые на ощупь, и чтобы сделать их цветные поверхности более яркими и реалистичными, 3D-отпечатки покрывают разными составами, например раствором морской соли, воском или цианоакрилатом. И тогда черепичная крыша на архитектурном проекте будет смотреться как черепица, а дерево - как дерево с присущими этому материалу текстурами. И все же, несмотря на реалистичность, речь идет о прототипах. Напечатанные шестеренки из гипса не смогут сколько-нибудь долго и надежно работать внутри механизма. Для того чтобы изготавливать методами 3D-печати промышленные образцы, нужна другая техника. И она, конечно, есть.
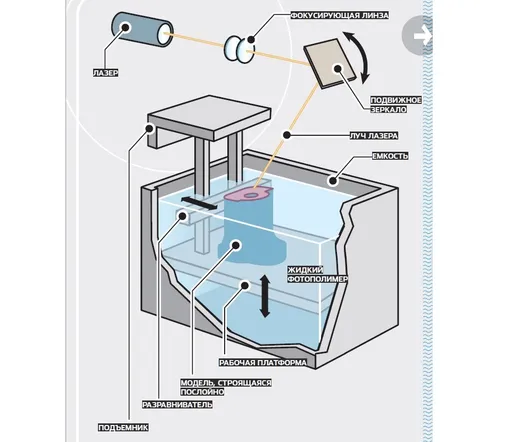
Пляшущий огонь
Говорят, можно бесконечно наблюдать за горящим огнем и за чужой работой. 3D-печать методом селективного лазерного спекания (SLS) представляет собой сочетание того и другого и, возможно, именно поэтому относится к зрелищам магическим и завораживающим. Мерцающее пламя, напоминающее маленький бенгальский огонь, бегает по поверхности, засыпанной одноцветным порошком, а на ней проступают темные контуры будущей детали. Технология здесь применяется также аддитивная, и модель растет слой за слоем. Только в отличие от холодного метода, в системе SLS мощный лазер не склеивает, а спекает порошок, формируя твердую деталь. Разновидностью этого процесса является прямое лазерное спекание металлов (DMLS), и здесь, в отличие от SLS, где работают с термопластиками, используются металлические порошки, например, на основе титана или нержавеющей стали.
Толщина слоя в DMLS может достигать 20 мкм, что позволяет изготавливать на 3D-принтерах мелкие сложные модели с минимальными допусками. На самом совершенном оборудовании этого типа, например, производимом немецкой компанией EOS, возможно создавать детали и механизмы, которые практически не требуют последующей обработки поверхностей — они готовы к работе в составе машин, в том числе в аэрокосмической индустрии.
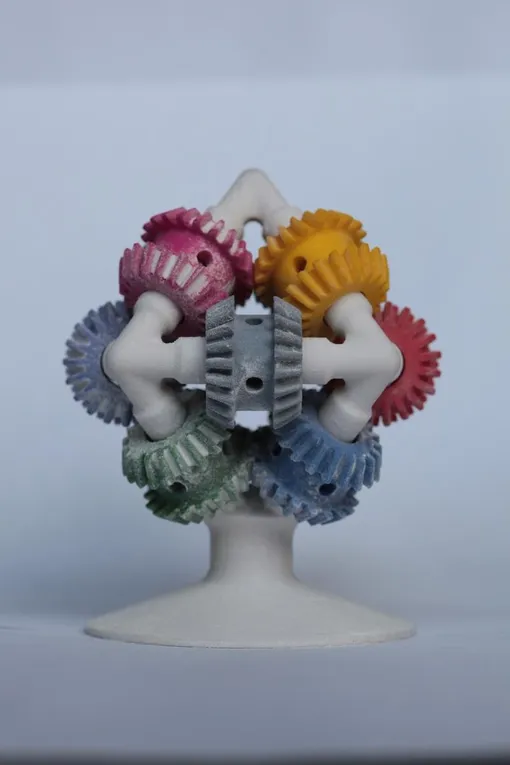
Печать без границ
Недавно команда исследователей под руководством Энди Кина и Джима Скэнлана из Университета Саутгемптона (Великобритания) объявила о создании первого в мире беспилотного самолета, фюзеляж которого изготовлен по технологиям SLS и DMLS. Чем, собственно, 3D-печать так заинтересовала авиаконструкторов? Дело в том, что эти технологии дают небывалую свободу в реализации конструкторских идей. Разрабатывая свой дрон с размахом крыльев 1,5 м, британцы решили использовать эллиптическую конструкцию крыла, применявшуюся когда-то на британском истребителе Supermarine Spitfire. Эта конструкция серьезно снижает лобовое сопротивление и дает тем самым большой выигрыш в маневренности, но... в свое время от нее отказались из-за чрезвычайной дороговизны изготовления этого сложного профиля в металле. 3D-печать снимает этот вопрос. Ей по силам любой профиль, заданный компьютерной моделью. Другое преимущество — это возможность быстрого перехода от компьютерного дизайна к летающему прототипу. Разработка и распечатка одного БПЛА занимает всего лишь неделю. При этом очередной беспилотник может отличаться от своего предшественника новыми элементами конструкции - достаточно лишь внести соответствующие изменения в CAD-модель.
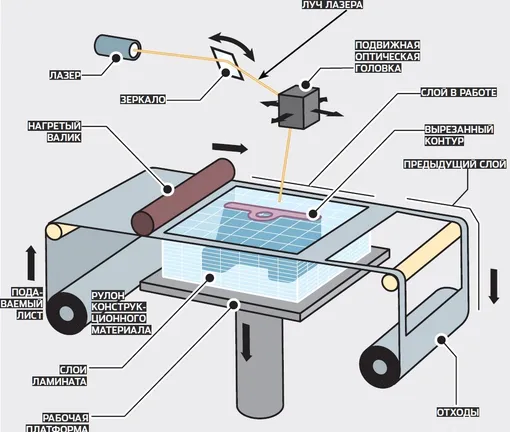
И это качество — пожалуй, самое ценное, что принесла трехмерная печать в проектирование. Проектируемый элемент можно многократно изменять, масштабировать, дорабатывать и получать на выходе деталь, работоспособность которой тут же проверяется в деле. При этом использование современных материалов позволяет добиваться от распечатанных моделей практически любой прочности, так что изготовление методом лазерного спекания лопастей авиатурбин — это никакая не фантастика, а вполне сегодняшний день.