Реверс-инжиниринг, или обратное проектирование, — процесс исследования оборудования или его компонента, который позволяет получить полную конструкторскую документацию. Сегодня он нередко включает и создание точной 3D-модели. По собранной информации потом легко совершенствовать оборудование и в краткие сроки изготавливать запасные детали. Все это сокращает стоимость ремонта и замены техники, способствует импортозамещению и, как результат, увеличивает скорость производства.
От металлических деталей до электроники: как реверс-инжиниринг помогает совершенствовать технологии в горной металлургии
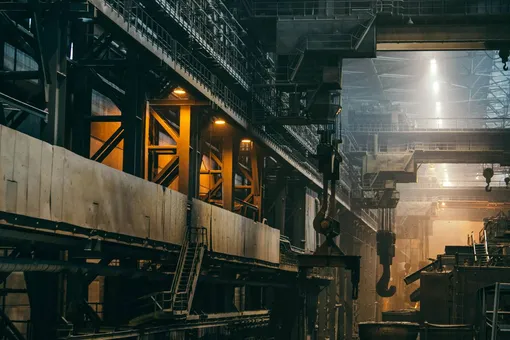
Такие технологии активно развивает Кольская горно-металлургическая компания (дочка Норникеля) — причем применительно не только к металлическим частям оборудования, но и к электронным компонентам. На руднике «Северный» уже работает оборудование, произведенное по воссозданной конструкторской документации.
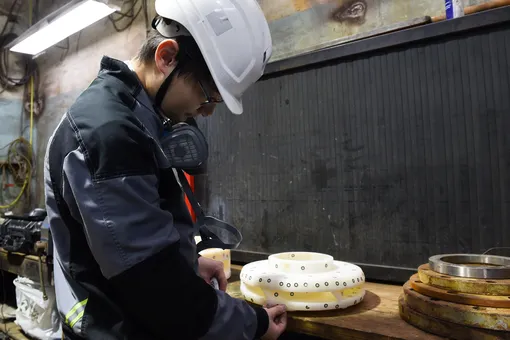
«Большое количество элементов, которые компания получила с помощью реверс-инжиниринга, применяются в цехе электролиза никеля или тестируются. В компании это уже выстроенный процесс», — объяснил директор департамента по инновациям и цифровым технологиям Кольского дивизиона Дмитрий Санников.
Процесс обратного проектирования
В среднем, обратное проектирование сложной детали занимает несколько недель. Весной 2024 года в цехе электролиза никеля на предприятии начали реверс-инжиниринг насосов Munsch-200 и Munsch-400. Так вот, на создание конструкторской документации тогда ушло примерно две недели.
Все начинается с полной разборки и очистки всех деталей оборудования. Чтобы сканер мог сориентироваться в пространстве и распознать компоненты, их обклеивают специальными метками. Их требуется много. Например, на Munsch-200 ушло 2,5 тысячи «наклеек».
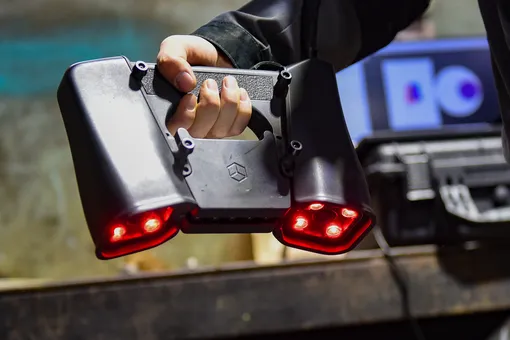
По меткам, которые считал сканер, на компьютере создается поле координат с облаком точек. Специальная программа «натягивает» на них сетку. Полученный «набросок» передают конструктору. Специалист проходит по всей модели в поиске неточностей и отклонений. Любое несоответствие или ошибка может сказаться на работе изделия. Этот же этап помогает по-настоящему углубиться в структуру объекта и собрать всю информацию об изделии, необходимую для документации.
В первую очередь в Кольском дивизионе так «обработали» детали и оборудование, поломка которых могла сказаться на технологическом процессе. Смотрели, что можно оперативно возместить, восстановить и заменить. Сейчас процедура отработана.
«Раньше мы смотрели, что можем возместить, восстановить, более оперативно поставить, чтобы технологический процесс не прерывался или ходимость изделия была более долгой. А сегодня это уже целая выстроенная процедура, которая включает в себя огромное количество заинтересованных сторон, и все участники между собой синхронизированы», — добавляет Дмитрий Санников.
Преимущества подхода
Разработчик не всегда может предсказать, как тот или иной компонент поведет себя в реальных рабочих условиях. Только продолжительное использование оборудования позволяет найти «тонкие» места. Когда на руках есть полноценная конструкторская документация и точная 3D-модель, гораздо проще рассчитать и улучшить компоненты оборудования под рабочие задачи.
В научном-техническом центре эксперты Норникеля проверяют, из какого материала лучше изготовить обновленное оборудование. Они оценивают, как изменение химического состава, структуры или свойств материала может сказаться на работе.
«Есть центр компетенций, эксперты которого четко знают, с помощью каких методов и технологий можно усовершенствовать или изготовить абсолютно уникальную деталь, которая нужна именно для нашего производства», — объяснил эксперт.
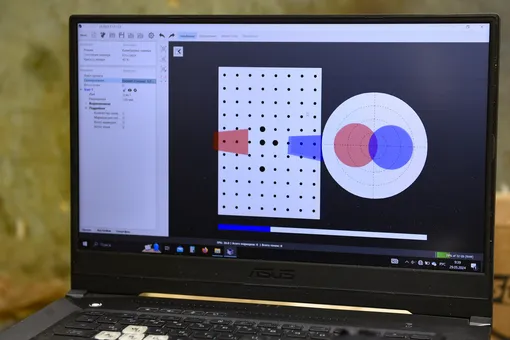
По словам начальника механослужбы цеха электролиза никеля Андрея Труханова, объемы замены деталей огромные: «Направление правильное. Сейчас коллеги используют технологию, чтобы оборудование в том числе модернизировать. Для компании это очень актуально. Мы заказываем тысячи запасных частей в год».
Основное преимущество технологии обратного проектирования — сокращение сроков и стоимости изготовления изделий. Готовые библиотеки документации и 3D-моделей открывают возможности для полноценного импортозамещения.
Многие компании, поставлявшие оборудование Кольскому дивизиону, покинули российский рынок. По словам главного менеджера департамента технологических инноваций «Норникель Спутник» Сергея Севагина, технология 3D-сканирования с целью создания полноценной документации уже применяется в Заполярном филиале «Норникеля», Кольской ГМК, горнорудной компании «Быстринское».
Рост и развитие
На базе проектно-конструкторского центра Кольского дивизиона планируется создать команду, которая займется выстраиванием системного подхода в развитии обратного проектирования, применения аддитивных технологий и 3D-моделирования. Сейчас 3D-сканированием сложных изделий занимается подрядная организация.
В 2023 году департамент по инновациям и технологиям определил, какие детали уже можно начать производить из полиамидов и пластикатов. Компания закупает профессиональное оборудование и планирует развитие собственного механообрабатывающего центра.
Единой базой конструкторской документации, созданной в Кольском дивизионе, смогут пользоваться все предприятия группы компании. А за счет передачи схем отечественным производителям, российские предприятия смогут запустить и более масштабное производство необходимых запасных деталей и оборудования.